Inside the Design of Benchmade: The Factory Collection
Published On
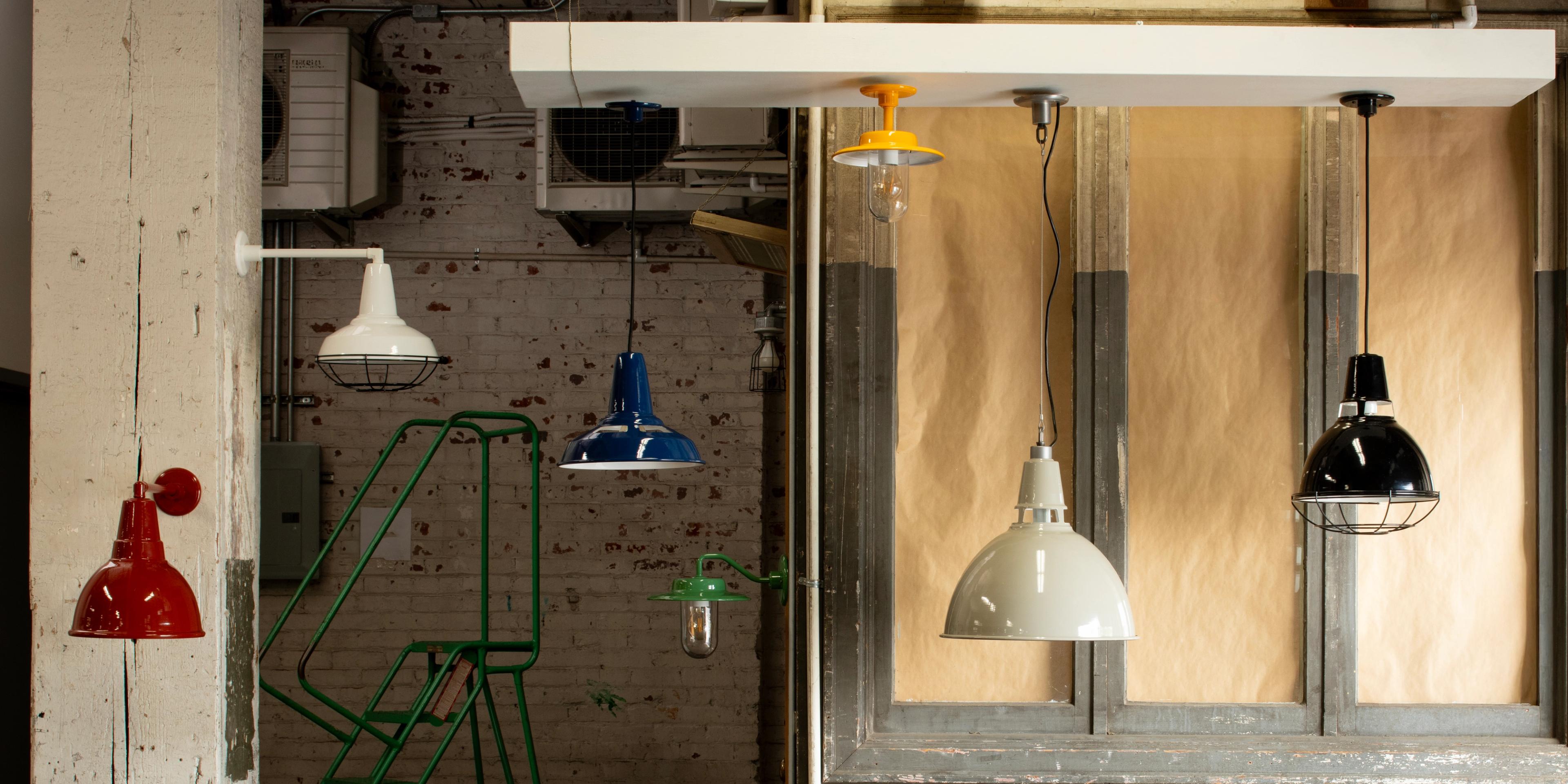
Creating a lighting fixture involves so much more than making something that’s beautiful. Before our product design team even puts pencil to paper, they consider the needs of our customers, our design values, and the legacy of our past creations. After that, we order all the parts—some are from the U.S., and others we source from trusted overseas vendors—and when they arrive at our Portland, Oregon factory, we finish and assemble them. If making a classic design together seems complicated, we can confidently say that the naming of this one was simple. Meet the Factory family.
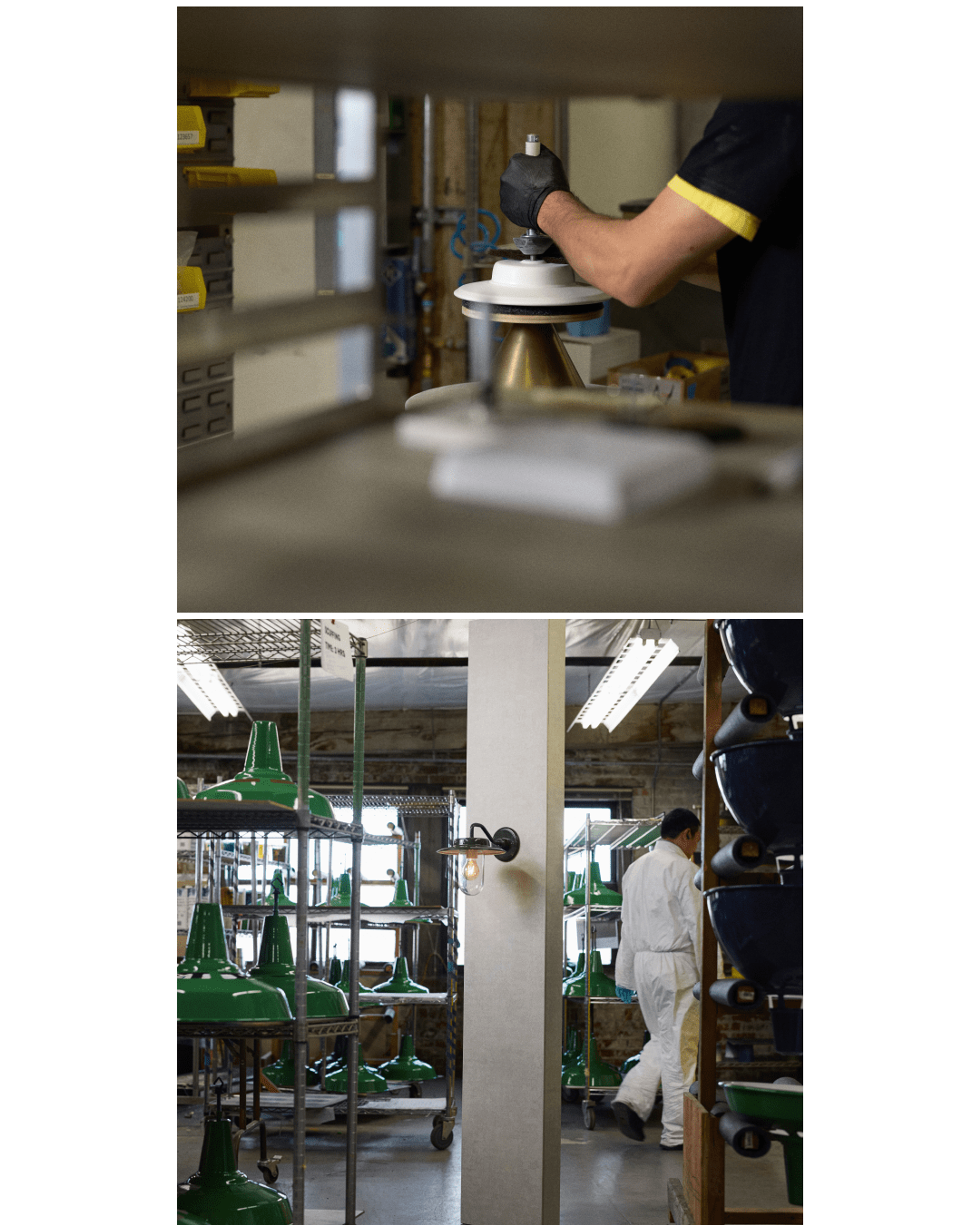
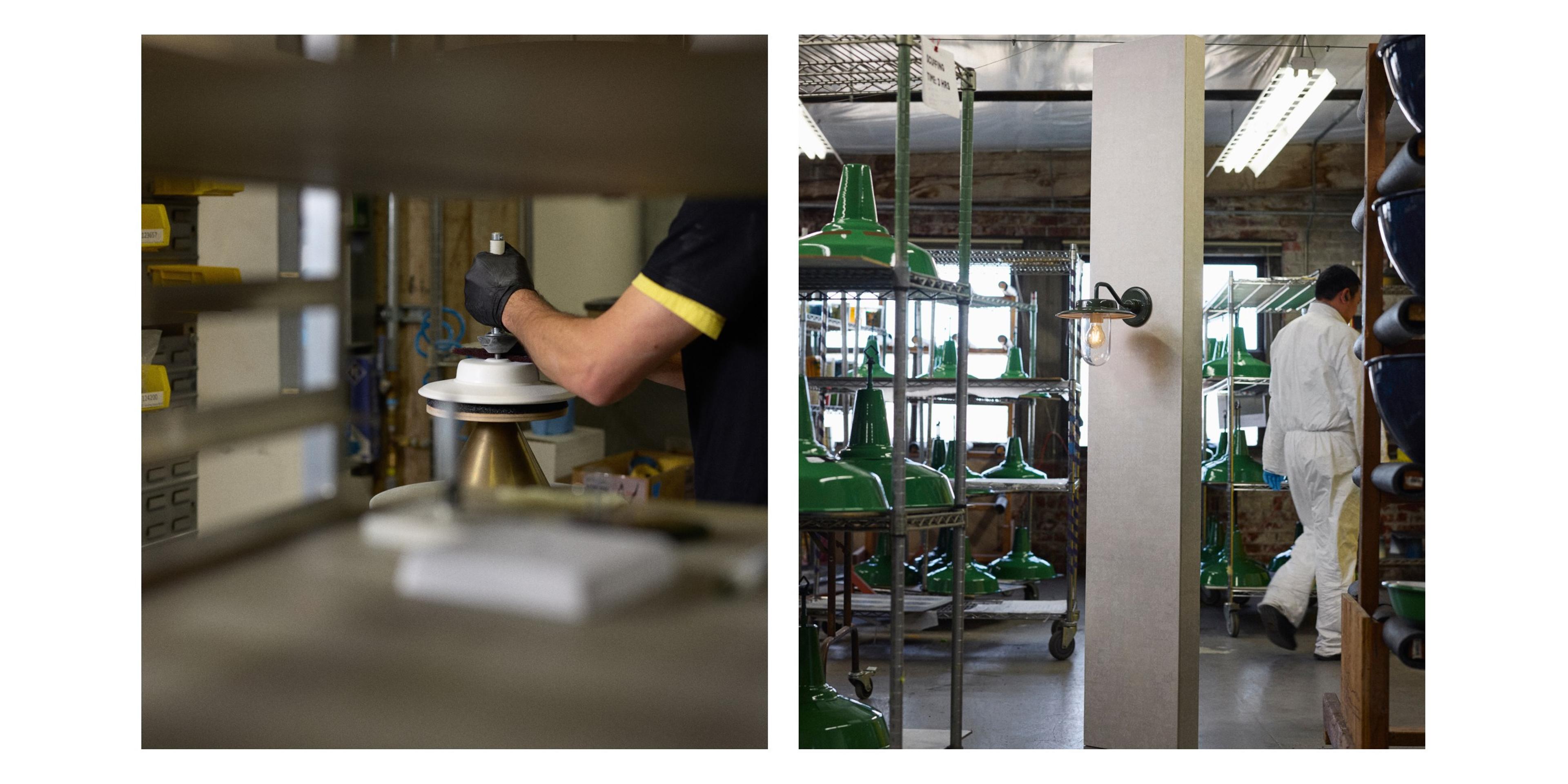
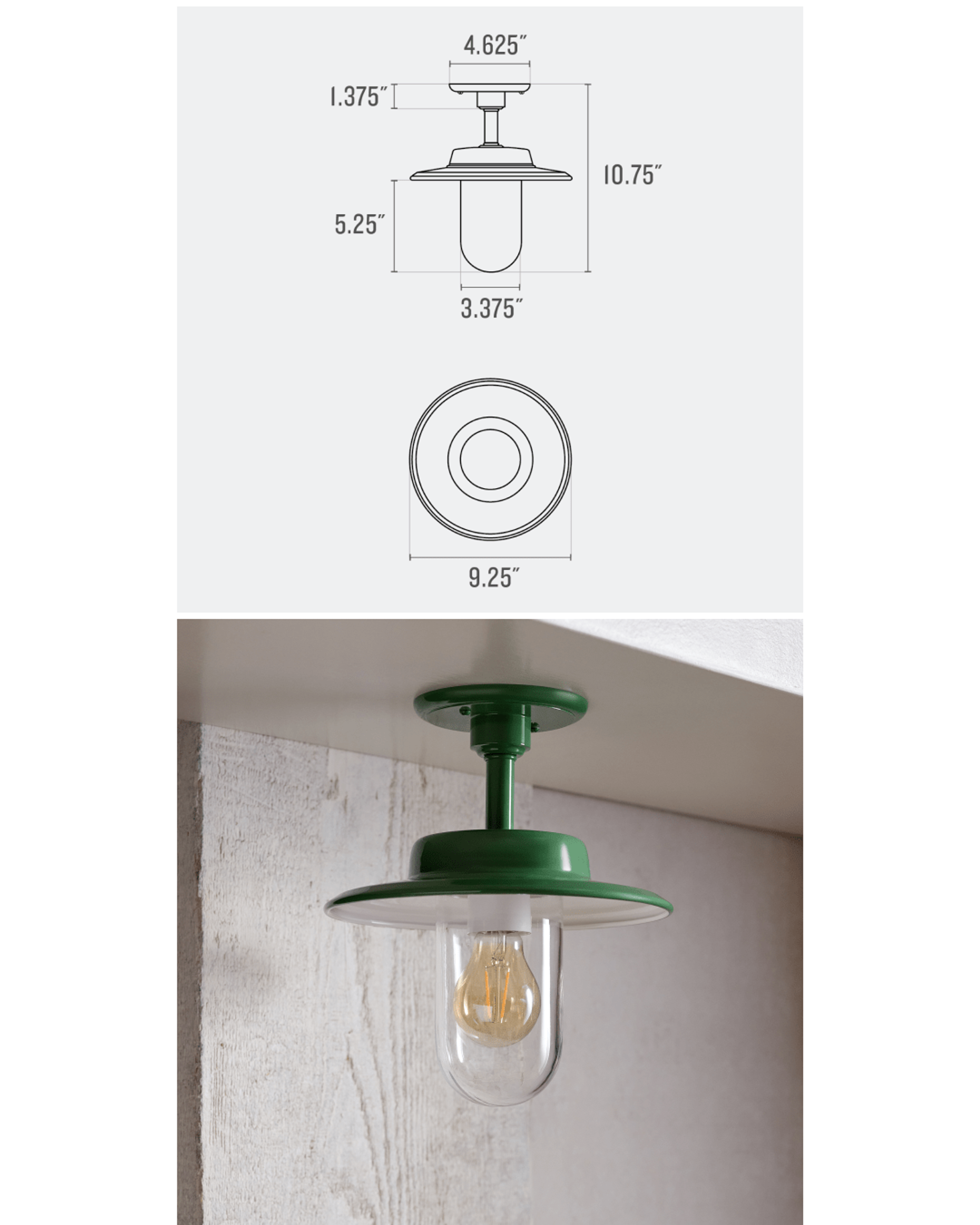
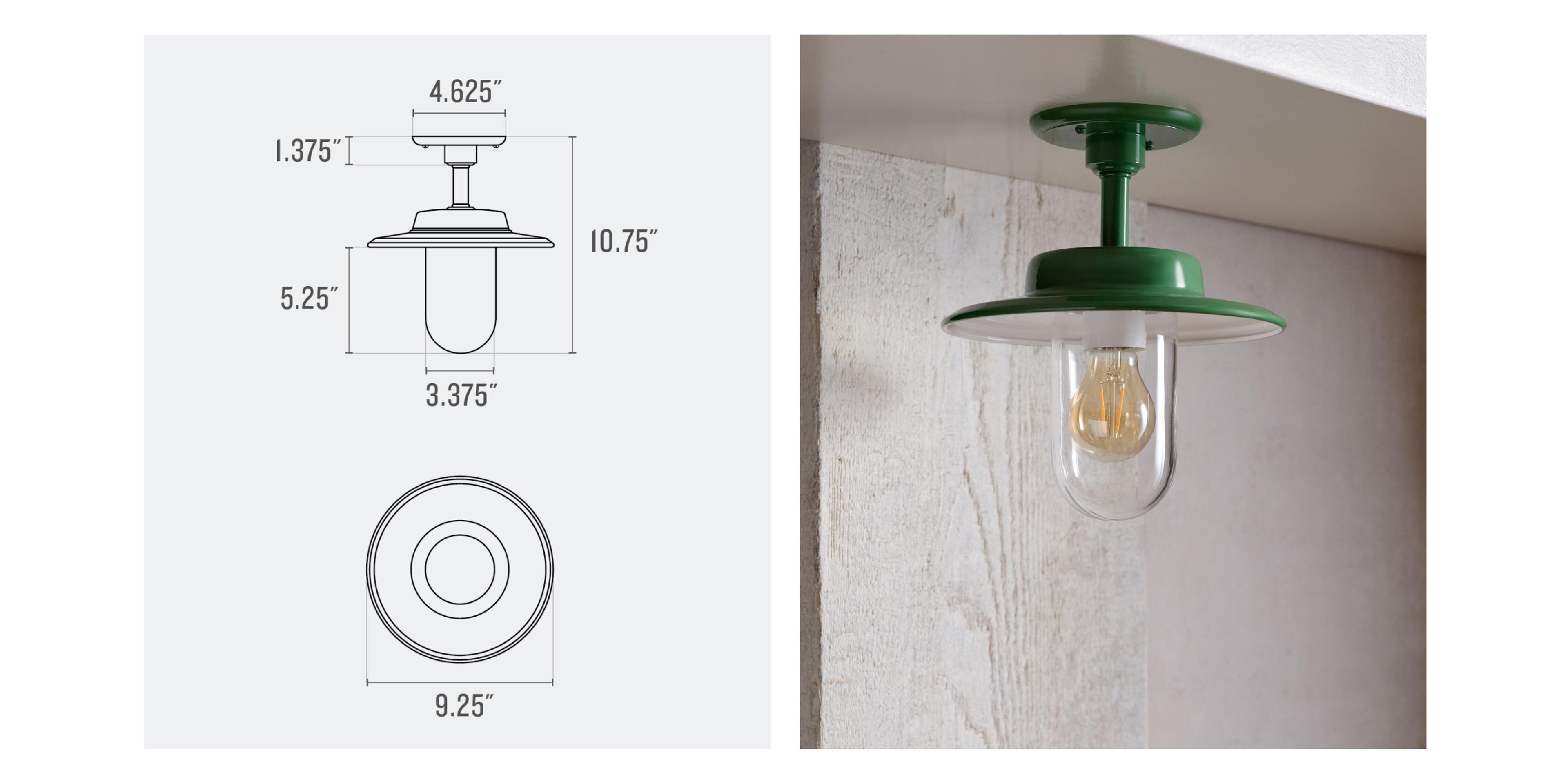
Inspired by the original RLM shade, our design team modeled our Factory fixtures after a series of vintage railway lights. There were a few design elements that we wanted to preserve—including the extra-wide bell opening for maximum light output, the top cutouts for heat release, and the industrial-grade construction—but at the top of the list? Its timeless form.
In the early 1900s, RLM (reflector luminaire manufacturer) shade inventor Reuben Berkley Benjamin used the principle of sound to inform the shape of a factory shade. The goal was to create a silhouette that distributed light rays evenly and efficiently throughout a space. Too wide of an angle, and the quality of light would diminish. Too narrow, and a harsh spotlight would appear. The end result? A perfectly balanced conical shape coated in enamel for its naturally reflective properties. While much has changed between then and now, the science behind the shade remains.
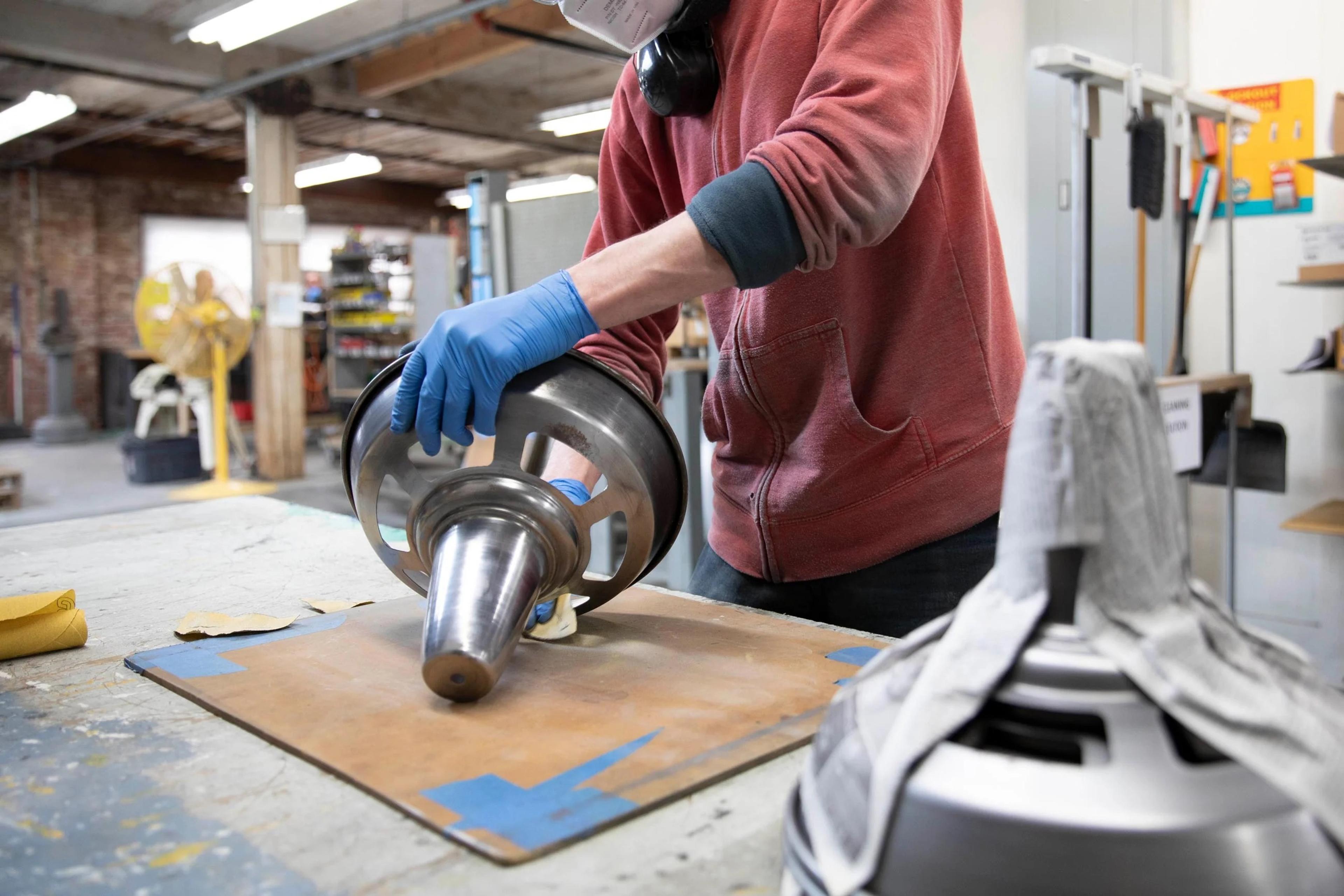
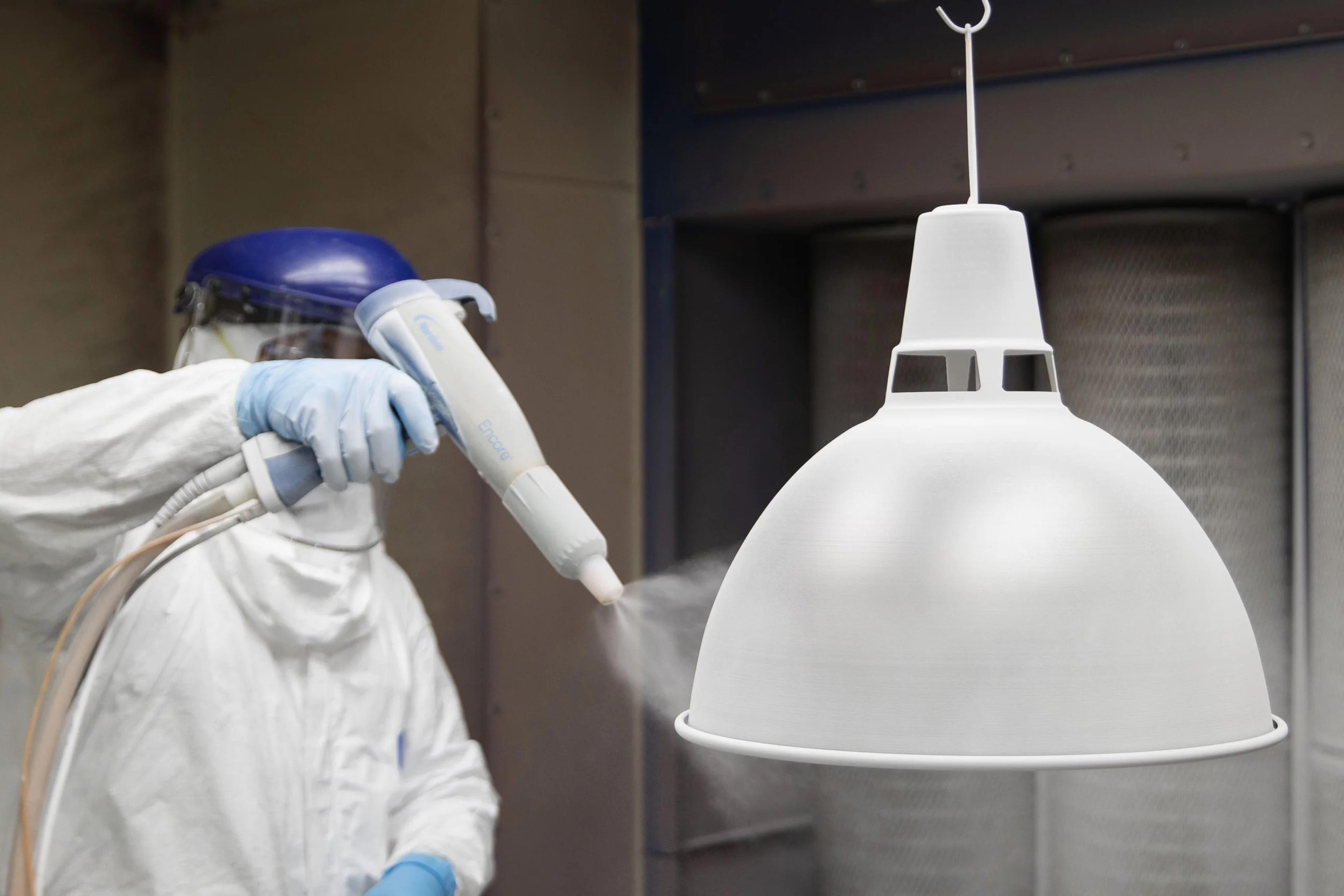
For our version, the goal was to create a silhouette which distributed light rays evenly and efficiently throughout a space. And of course, we’d finish and assemble it in our hometown factory. Today, our Factory fixtures are made from hand-spun steel on a custom RLM tool unique to Schoolhouse. Once the raw shades are received in-house, we sand, then blast them with tiny glass beads on the fourth floor of our factory. The process of bead-blasting first allows the powder color to evenly coat each shade.
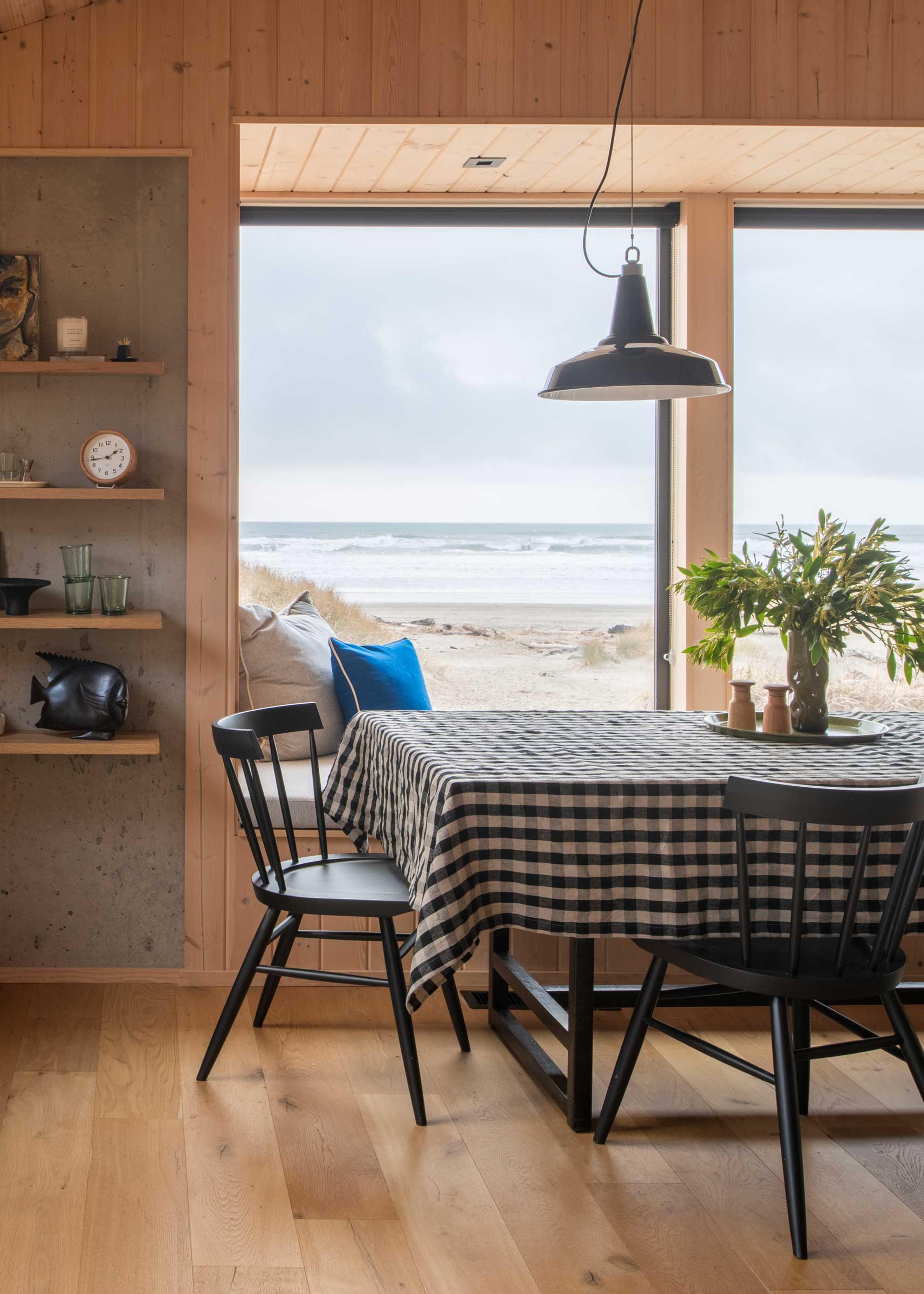
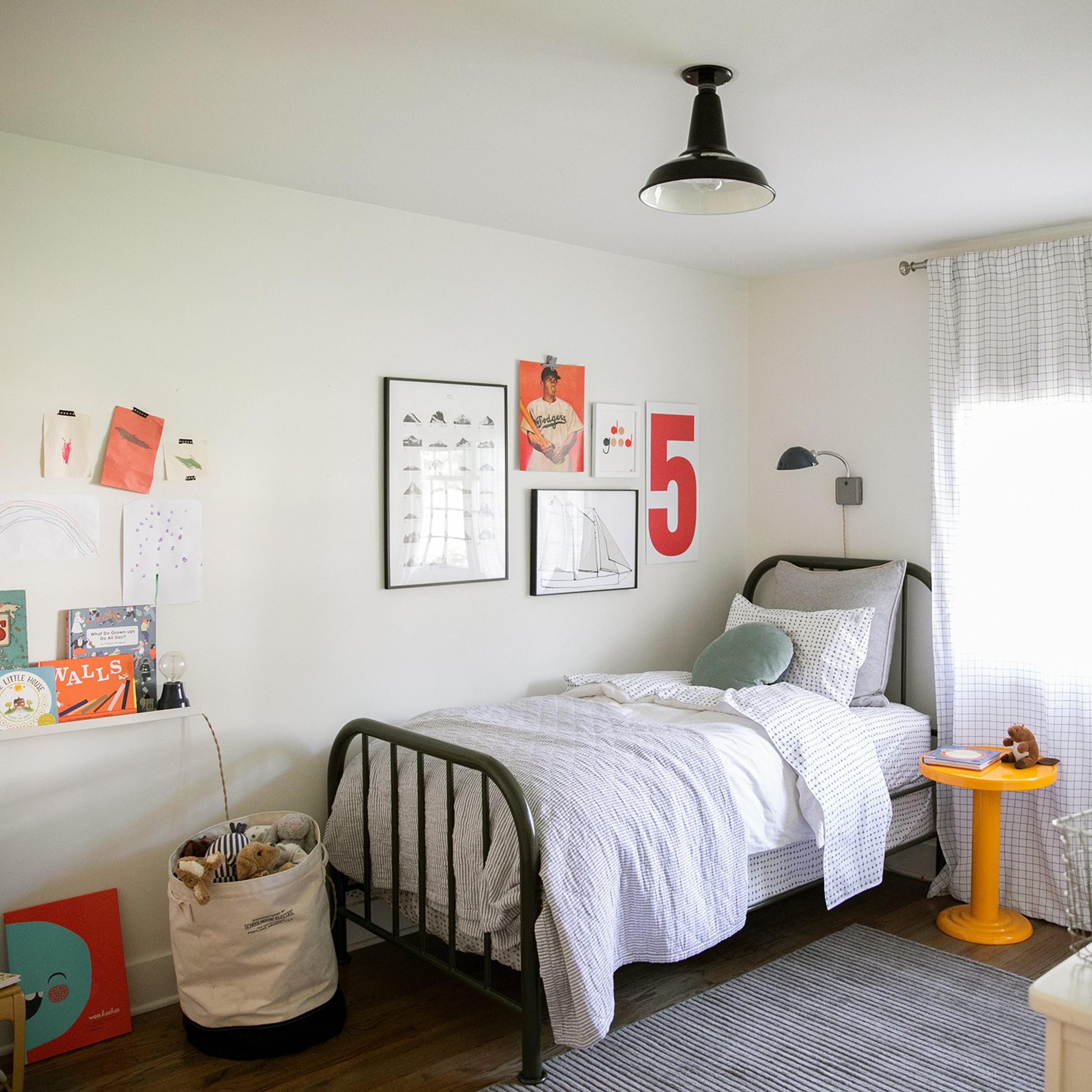
Once the shades are dry, they make their way to assembly on our second floor where century-old wood floors, towers of cardboard boxes, spools of colored wires, and giant bubble wrap rolls set the scene. Several clocks tick away in unison as they’re tested for accuracy. The first assembly station collects all the necessary parts, inspects them for quality, and starts the basic wiring to make either a Factory sconce, surface mount, or pendant. The next bench takes these parts and assembles the fixture. The final team tests each light to ensure it meets our standards before packaging it up for delivery—straight from our factory and right to your door.
A quiet nod to the beauty of American craft, these fixtures are a study in simplicity done right. Built the old-fashioned way—by hand, with care—they balance utility with timeless design. Though they may be straightforward in their function, bringing them to life is no small task. As the old adage goes, “Simplicity is the ultimate sophistication."
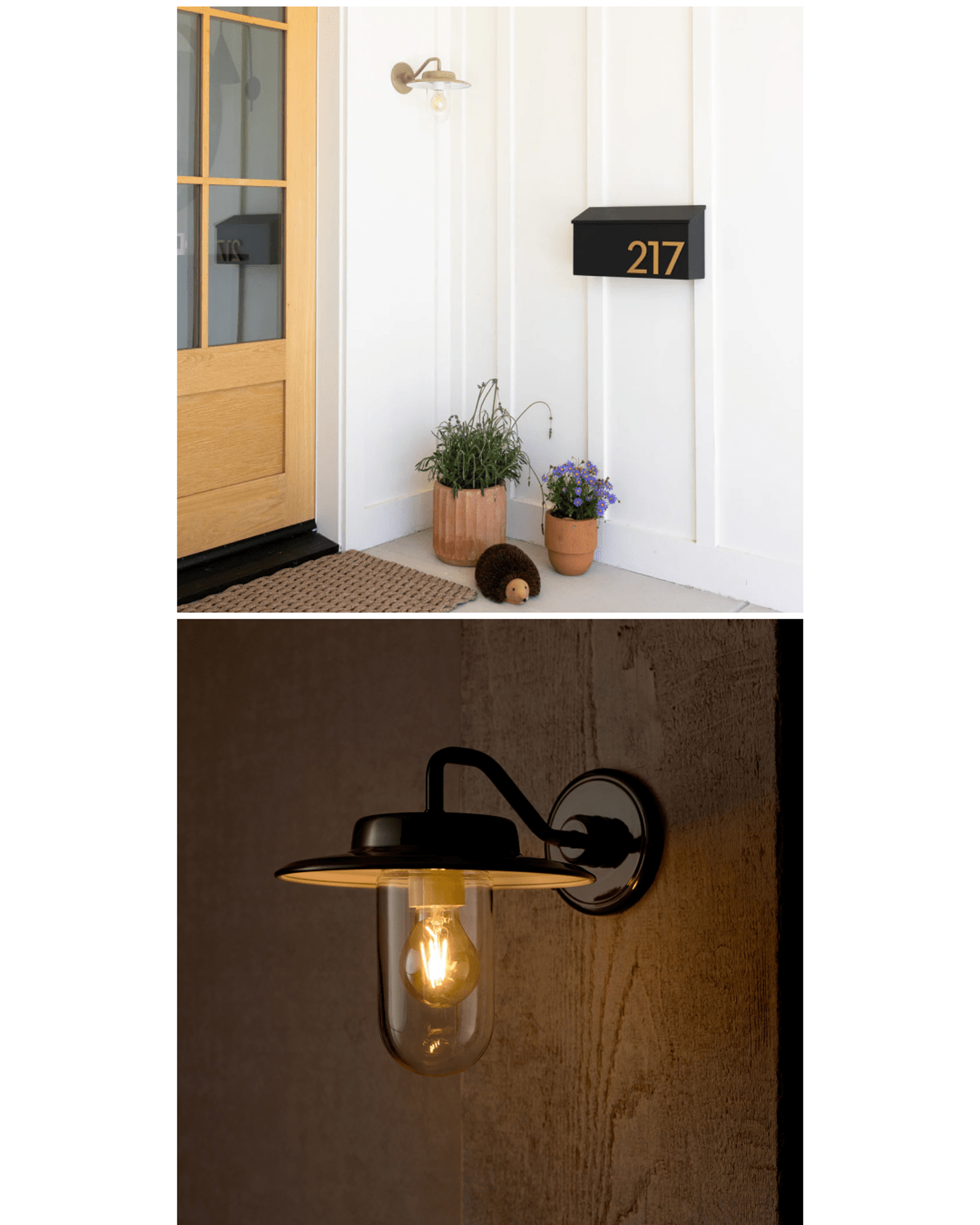
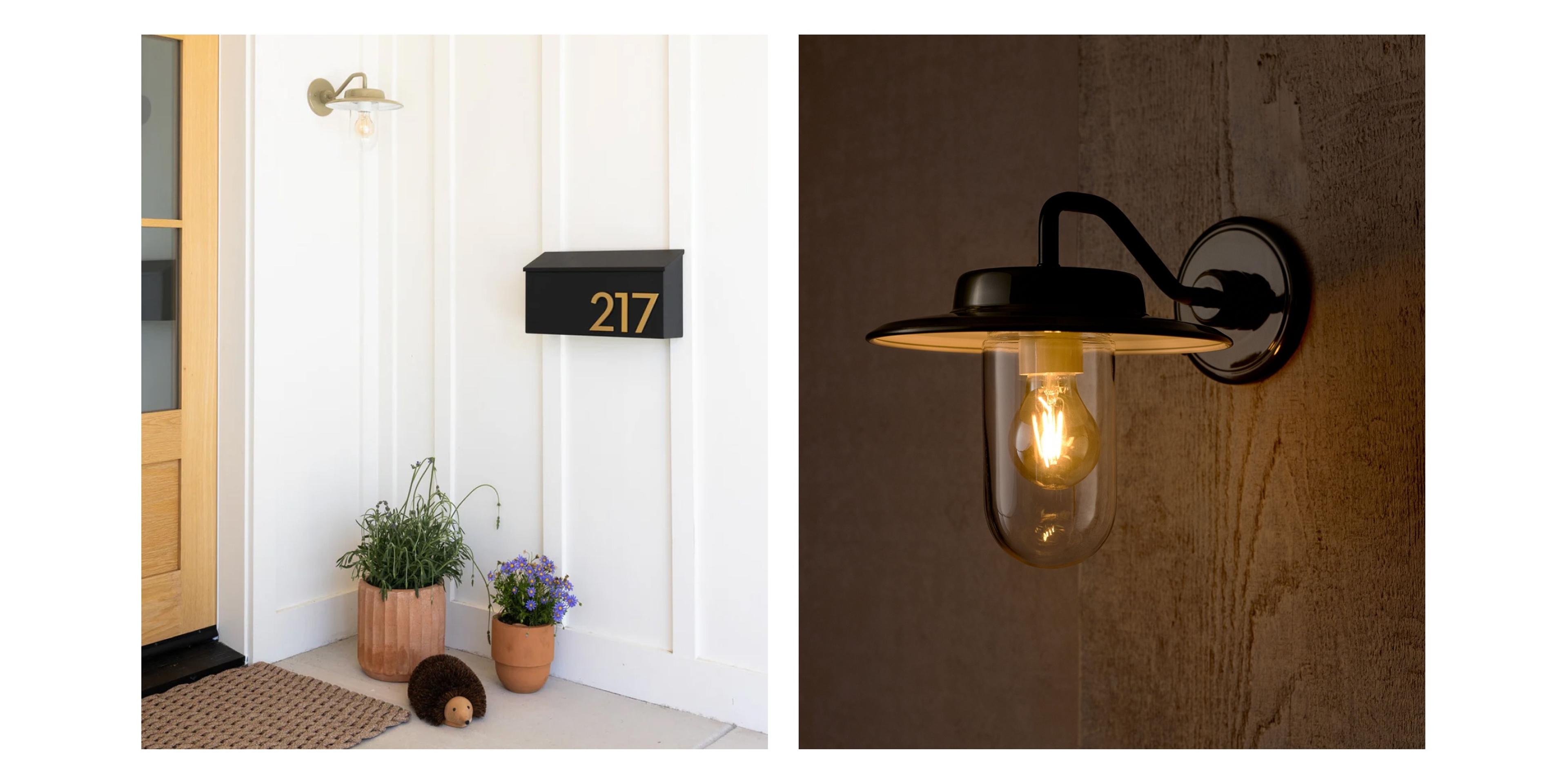
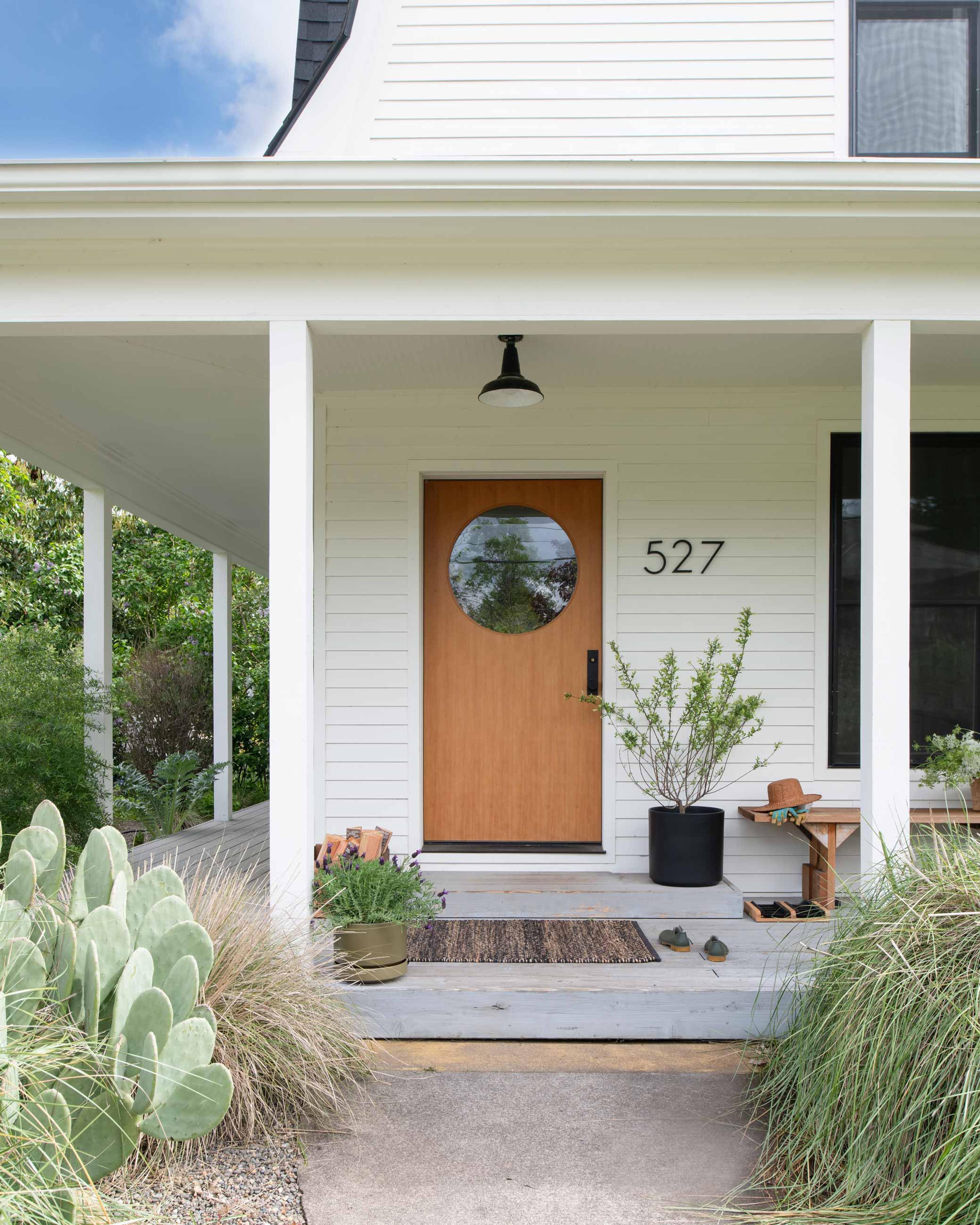